Dicke Bleche mit geringer Laserleistung schweißen
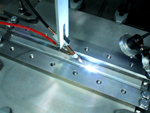
Mehrlagen-Engstspaltschweißverfahren an einem 50 mm Blech / Bildquelle: Fraunhofer IWS Dresden
50 mm dickes Blech mit nur 5 kW Laserleistung schweißen – wie geht das? Bauteile mit großen Blechdicken sind in einer Vielzahl von Hochtechnologieanwendungen zu finden. Das schweißtechnische Fügen der Bauteile stellt eine große Herausforderung und wesentliche Kostenposition im Fertigungsprozess dar. Das Fraunhofer IWS Dresden hat deshalb ein neues Verfahren zum Schweißen von Blechen mit Dicken bis 50 mm entwickelt.
Beispiel einer 50 mm Mehrlagen-Engstspaltschweißnaht (links Stahl, rechts Aluminium) / Bildquelle: Fraunhofer IWS Dresden
Windkraftanlagen, Turbinen und deren Gehäuse, aber auch chemische Apparate lassen sich zukünftig nur dann effizient betreiben, wenn sowohl die Grenzen der mechanischen als auch die der thermischen Belastbarkeit ausgereizt werden. Für die eingesetzten Fügeverfahren besteht die Herausforderung vor allem in der Minimierung der thermischen Schädigung des Werkstoffgefüges, um die technologischen Eigenschaften des Werkstoffes weiterhin zu garantieren. Mit dem im Fraunhofer IWS entwickelten Verfahren, dem laserbasierten Mehrlagen-Engstspaltschweißen, können Blechdicken bis 50 mm mit Laserleistungen kleiner 5 kW geschweißt werden. Möglich wird dies durch Festkörperlaser mit exzellenter Strahlqualität. Die bisher sanduhrförmige Kaustik des Laserstrahls ist bei diesen Strahlquellen so schlank, dass sie in extrem schmale und tiefe Spalten eingestrahlt werden kann, ohne die angrenzenden Flanken der Fuge aufzuschmelzen. Somit erfolgt der Energieeintrag durch den fokussierten Laserstrahl sehr konzentriert, lokal begrenzt bis in den Spaltgrund und die Fuge kann Lage für Lage aufgefüllt werden. Dieser neue Ansatz für die Laserstrahltechnik ist Gegenstand aktueller Forschungsarbeiten am Fraunhofer IWS in Dresden.
Der Vorteil des Verfahrens ist nicht nur aus energetischer Sicht sondern auch hin-sichtlich der im Vergleich zum Schweißen mit Elektronenstrahl deutlich reduzierten Investitionskosten enorm. Zudem lassen sich die prozesstypischen Vorteile des Laserstrahlschweißens wie geringer Winkelverzug, geringe Streckenenergie und minimaler Verbrauch von Schweißzusatzwerkstoff realisieren.
Vergleicht man die laserstrahlgeschweißten Bleche mit Blechen, die üblicherweise mit konventionellen MSG-Verfahren gefügt werden, fällt vor allem die sehr schlanke, nahezu flankenparallele Schweißnaht auf. Bauteile, die aufgrund des Schweißverzuges beim MSG-Schweißen aufwendig nachbearbeitet werden mussten, profitieren beim neuen Verfahren von abnehmendem Verzug mit zunehmender Blechdicke. Schrumpfspannungen quer zur Schweißnaht, denen gerade bei dickwandigen Bauteilen schwer zu begegnen ist, werden durch den neuen Verfahrensansatz erstmals kontrollierbar.
Die neue Qualität der Schweißnahtgeometrie ist auch der Schlüssel dafür, bisher für das Schweißen großer Bauteildicken ungeeignete Werkstoffe, wie beispielsweise kaltrissgefährdete Legierungen, für Schweißanwendungen zugänglich zu machen. Auch für heißrissgefährdete Aluminium-Legierungen eröffnen sich neue Perspektiven, da erstmals der metallurgisch erforderliche Schweißzusatzwerkstoff bis in die Schweißnahtwurzel eingetragen werden kann. Ebenfalls neuartig ist die Möglichkeit, das Dickblechschweißen vor Ort auf einer Baustelle einzusetzen, etwa im Anlagen- oder Schiffbau. Durch die geringe Laserleistung und der hohen Energieeffizienz der verwendeten Laserquellen, steht einem mobilen Einsatz zum Beispiel in Kraftwerken zu Reparaturzwecken nichts im Wege.
www.iws.fraunhofer.de
Aktuelle Onlineartikel
-
02. 07. 2025 Vom Reaktordesign bis zum gedruckten Schnitzel – KIT kürt die besten Innovationen
-
02. 07. 2025 Kompostierbares Einmalgeschirr
-
01. 07. 2025 Energieverbrauch mit Phasenwechselmaterialien reduzieren
-
01. 07. 2025 Neues Produktionsverfahren für Metall-Polymer-Stromkollektoren
-
27. 06. 2025 Neue Aluminiumlegierungen für die Wasserstoffwirtschaft
-
24. 06. 2025 VOA gestaltet ESTAL-Kongress 2025 in Griechenland mit