Graphene as a corrosion protecting system
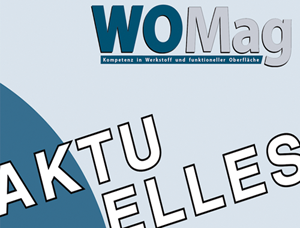
The carbon material graphene is not only the great hope for future electronics, it provides even at today's components to protect against corrosion. Because the researchers of the Australian Monash University and the American Rice University report, a thin, almost invisible coating copper graph makes it much more resilient - and that, although normal graphite corrosion benefiting from them.
Mainak Majumder, a researcher at the Faculty of Engineering, Monash University emphasizes that the research approach of his team is nearly 100 times more resistant than untreated copper. Other researchers in this area provide a factor of five or six, so that's a really big jump. Such anti-corrosion coatings may also occur on a large scale for vessels used, say the engineers. On graphene nanostructures are high hopes for the electronics. The Australian-American team says the carbon material could also revolutionize the field of anti-corrosion coatings. Parama Banerjee, chemical engineer at Monash University, called the nanomaterial a magical material. For whereas previously used polymer coatings are scratch-prone, which may affect their protective action, the extremely thin graphene coating is much harder to damage.
The applied by chemical vapour deposition graphene layer is invisible and does not change appearance of the underlying metal or what it feels like this. As potential scope Banerjee looks in addition to copper in electronics in particular ships. Because as copper protective coating graphene has proved itself in tests in salt water. In a country like Australia, which is surrounded by oceans, it is particularly important that such an atom-thin coating can provide protection in such environments, the researcher said.
The farther the team examines whether a graphene coating is also suitable as corrosion protection for other metals. In addition, the scientists want to lower the temperature needed for applying the coating compared to the currently required 800 °C to 900 °C, as this would facilitate the production and thus increase the market potential.
Aktuelle Onlineartikel
-
29. 04. 2025 MIT macht Keramik und Glas jetzt dehnbar
-
28. 04. 2025 Die ultraschnelle elektrische Aufladung von Flüssigkeiten erforschen
-
28. 04. 2025 NMI, TU Darmstadt und Black Drop entwickeln verbesserte Biotinte
-
28. 04. 2025 Schutzschild aus Nanopartikeln für langlebigere Leuchtstoffe in der Hightech-Anwendung
-
28. 04. 2025 Kautschukmischungen mit alternativen Antioxidantien – neues Projekt
-
25. 04. 2025 Wie mit Hilfe von Methan und CO2 der Plastikverschmutzung begegnet werden kann