Environmentally friendly corrosion protection for rivets
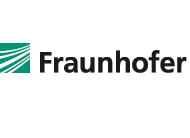
New lightweight design concepts help to reduce the energy that is consumed by cars and rail vehicles. A lower intrinsic weight means lower fuel consumption for cars with combustion engines, longer travel distances for modern electric cars, or a lower required drive power for rail vehicles.
The new combinations of materials, which make this possible comprise aluminum alloys, high-strength steel, and fibre reinforced plastics. These heterogeneous materials are joined together mechanically using rivets and glued with adhesives. The rivet elements must be able to withstand very high loads: Vibrations at speeds of more than 100 km/h, aggressive ambient air, high temperatures, and a strong electrochemical potential field due to the very different electrochemical potentials of the incorporated materials.
Effective protection of the rivets against corrosion and wear reduces the maintenance effort and lowers the risk of material failure.
The Fraunhofer Institute for Electron Beam and Plasma Technology FEP has developed a deposition process for efficiently coating bulk rivets with corrosion protection layers. In a slowly rotating drum the rivets are continually and gently mixed and simultaneously coated in the metal vapour. In a pilot plant up to 30 kg rivets can be coated with a multilayer coating stack using plasma enhanced high-rate deposition and pulse magnetron sputtering. By applying the two vacuum technologies a layer system of alternating aluminum layers of about 1 µm thickness and much thinner sputtered diffusion barrier layers can be achieved. Standard test procedures such as the VDA corrosion test (VDA 621-415) demonstrated the excellent corrosion resistance of the coated rivets. Vacuum coating has two major advantages over the galvanic coating methods used until now: Firstly, it is eco-friendly with regard to the materials used. Secondly, hydrogen embrittlement, which can cause fatigue in high-strength steel and titanium substrates, does not occur in vacuum coating processes.
Dr. Heidrun Klostermann, head of the business unit „Coating of components“ at Fraunhofer FEP, describes further potential applications for the process: Besides rivets, other small mass-produced components such as screws / bolts, pins, balls, links, or nails of size between 0.2 and 4 cm can be coated as bulk products. By combining different vacuum processes a broad range of materials can be deposited. Hence, the technology is ready for plenty of other coating tasks for bulk products.“
Aktuelle Onlineartikel
-
29. 04. 2025 MIT macht Keramik und Glas jetzt dehnbar
-
28. 04. 2025 Die ultraschnelle elektrische Aufladung von Flüssigkeiten erforschen
-
28. 04. 2025 NMI, TU Darmstadt und Black Drop entwickeln verbesserte Biotinte
-
28. 04. 2025 Schutzschild aus Nanopartikeln für langlebigere Leuchtstoffe in der Hightech-Anwendung
-
28. 04. 2025 Kautschukmischungen mit alternativen Antioxidantien – neues Projekt
-
25. 04. 2025 Wie mit Hilfe von Methan und CO2 der Plastikverschmutzung begegnet werden kann