Zusätzliche Drehachse soll Kosten im Triebwerksbau senken
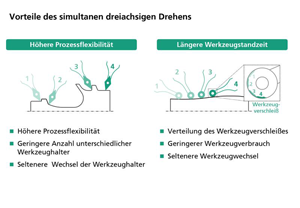
Beim Drehen von Triebwerkskomponenten aus hochwarmfesten Werkstoffen muss oft schon nach wenigen Minuten das Werkzeug gewechselt werden – entweder weil es bereits verschlissen ist oder weil aufgrund der Bauteilgeometrie ein anderer Werkzeugwinkel eingestellt werden muss. Für eine einzige Turbinenscheibe werden beispielsweise weit mehr als 100 Schneidplatten verbraucht, eine Vielzahl an unterschiedlichen Werkzeughaltern kommt dabei zum Einsatz. Auf der EMO Hannover 2013 zeigt das Fraunhofer-Institut für Produktionstechnologie IPT vom 16. bis 21. September eine Alternative zu dieser aufwändigen und kostspieligen Art der Herstellung: Mit dem dreiachsigen Drehen können Unternehmen in Zukunft bis zu 30 % der Bearbeitungskosten einsparen.
Viele rotationssymmetrische Bauteile, die in Turbomaschinen zum Einsatz kommen, werden durch eine Drehbearbeitung hergestellt. Turbinenscheiben, -gehäuse oder Triebwerkswellen aus Werkstoffen mit extrem hoher Festigkeit, so genannten Superlegierungen, sind oft sehr komplex geformt und dadurch extrem teuer. Die aufwändigen Geometrien erfordern beim herkömmlichen Drehen eine Vielzahl an Werkzeugwechseln und verschiedenen Werkzeughaltern, um die komplexen Konturen des Bauteils zu erzeugen. Die ständigen Werkzeugwechsel führen zu langen Nebenzeiten in der Maschine und erhöhen so die Herstellungskosten immens. Auch durchgehende, lange Schnitte sind bei den schwer zerspanbaren Werkstoffen kaum möglich, da das Werkzeug bereits nach wenigen Minuten verschlissen ist. Dann kann das Material nur noch ungenau abgetragen und die erforderliche Formgenauigkeit und Oberflächengüte nicht mehr erzielt werden.
Das simultane, dreiachsige Drehen kann hier Abhilfe schaffen. Der Winkel, in dem das Drehwerkzeug auf das Metall trifft, wird dabei nicht mehr wie bisher durch die Geometrie des Werkzeughalters bestimmt. Stattdessen übernimmt eine dritte, rotatorische Achse, zusätzlich zu den beiden üblichen, translatorischen Achsen X und Z die Einstellung des Winkels.
Marktübliche Dreh-Fräs-Zentren besitzen bereits solch eine dritte rotatorische B-Achse. Sie wird jedoch heute für das Drehen noch nicht genutzt, sondern nur für den Fräsprozess – und das, obwohl dadurch auch die Flexibilität der Drehoperationen deutlich erhöht werden könnte und die Werkzeughalter seltener gewechselt werden müssten. Indem außerdem die Werkzeugschneiden gezielt mit unterschiedlichen Berührungspunkten in das Material eingreifen, verteilt sich auch der Werkzeugverschleiß über die gesamte Schneide und der Werkzeugverbrauch nimmt insgesamt deutlich ab.
Das Fraunhofer IPT arbeitet zurzeit daran, die B-Achse vollständig für den Drehprozess nutzbar zu machen. Neue Modelle zur Beschreibung des Drehprozesses, und die passenden Methoden zur Prozessauslegung sollen den industriellen Einsatz schon bald in greifbare Nähe rücken. So lassen sich nicht nur der Werkzeugverschleiß und die Anzahl der Werkzeugwechsel optimieren, die Prozesse werden auch flexibler bei gleichzeitig sinkenden Bearbeitungskosten.
www.ipt.fraunhofer.de
Aktuelle Onlineartikel
-
02. 07. 2025 Vom Reaktordesign bis zum gedruckten Schnitzel – KIT kürt die besten Innovationen
-
02. 07. 2025 Kompostierbares Einmalgeschirr
-
01. 07. 2025 Energieverbrauch mit Phasenwechselmaterialien reduzieren
-
01. 07. 2025 Neues Produktionsverfahren für Metall-Polymer-Stromkollektoren
-
27. 06. 2025 Neue Aluminiumlegierungen für die Wasserstoffwirtschaft
-
24. 06. 2025 VOA gestaltet ESTAL-Kongress 2025 in Griechenland mit