Aktuelle Highlights
Mittels Galvanotechnik zu Uhrspiralen der nächsten Generation
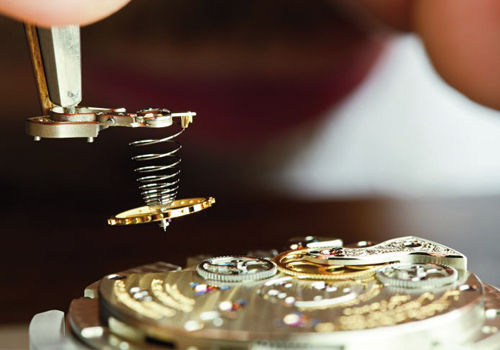
Die Unruh ist das Herzstück jedes mechanischen Uhrwerks. Die feine Feder besteht gewöhnlich aus gegossener, gewalzter Nivarox-Legierung. An der Empa werden Unruhfedern auch auf galvanischem Weg hergestellt (Bild: A. Lange & Söhne)
Empa-Forscher Johann Michler und sein Team befassen sich unter anderem mit der zunehmenden Miniaturisierung von Bauteilen – auch solchen, auf die wir täglich angewiesen sind. Als Nebenprodukt ihrer Forschung entstehen völlig neuartige Uhrspiralen, die schon bald in Schweizer Zeitmessern eingesetzt werden könnten (Titelbild).
Angewandte Forschung ist nicht immer von der Industrie initiiert – aber sehr oft entsteht dabei trotzdem ein Ergebnis, das rasch industriell umgesetzt werden kann. Ein Beispiel dafür ist am Empa-Standort Thun zu sehen: Sehr kleine Uhrspiralen liegen dort in den Schaukästen des Laboratory for Mechanics of Materials & Nanostructures. Diese Spiralen – das schlagende Herz jedes mechanischen Uhrwerks – sind keine gewöhnlichen Bauteile. Sie sind nicht aus den berühmten Nivarox-Drähten hergestellt, sondern werden aus einer kalten, wässrigen Salzlösung galvanisch – oder elektrochemisch – in der gewünschten Form abgeschieden. Längst ist die Herstellung im Empa-Labor aus den ersten Vorversuchen herausgewachsen. Die galvanisch hergestellten Spiralen werden regelmäßig an die Forschungsabteilung eines großen Schweizer Uhrenherstellers geliefert und dort in Prototyp-Uhrwerke eingebaut. Die Uhrwerke laufen. An der Ganggenauigkeit und Langzeitstabilität werde noch gearbeitet, heißt es.
Noch vor wenigen Jahren war die Empa häufig auf Partner angewiesen, die bestimmte Prozessschritte übernahmen. Inzwischen ist das Know-how für die gesamte Herstellung im Labor vereint. Laetitia Philippe, welche die Herstellung der Spiralen betreut, erläutert die Produktionsschritte. Ausgangsmaterial ist ein Siliziumwafer, wie er in der Herstellung von Computerchips und Solarzellen verwendet wird. Dieser Wafer wird zunächst mit einer leitfähigen Goldschicht und dann mit einer dünnen Schicht lichtempfindlichen Lacks überzogen. Dann wird die Form der Spirale darauf projiziert und die belichteten Stellen des Lacks herausgeätzt. Nun kann auf der leitfähigen Goldunterlage die gewünschte Legierung galvanisch abgeschieden werden.
Dieser entscheidende Prozessschritt erfordert die Einstellung einiger Prozesskennwerte: ausreichende und steuerbare Umwälzung der wässrigen Lösungen, die richtige Temperatur, einige organische Zusatzstoffe sowie Strom in der korrekten Stärke und – falls es Wechselstrom ist – in der passenden Form. Schließlich gilt es, die Spiralen aus der galvanischen Form herauszulösen. Zunächst kontrolliert die Forscherin Laetitia Philippe mit einem Lichtmikroskop, ob die Spiralformen korrekt mit Metall gefüllt sind. Dann wird die Oberseite der Form feinpoliert, damit alle Spiralen eine definierte Dicke haben, das Ergebnis wird per Röntgenfluoreszenzanalyse kontrolliert.
Schließlich wird der Lack mit einem Sauerstoffplasma entfernt, der Siliziumwafer mit einer starken Lauge weggeätzt und die Goldschicht aufgelöst. Die übrig bleibenden Spiralen müssen dann noch für einige Stunden einer speziellen Oberflächenbehandlung unterzogen werden, um Grate und überstehende Metallreste zu entfernen. Die so entstandenen, optisch fehlerfreien Spiralen gehen dann zur Prototypenfertigung ins Uhrenlabor.
Bild 2: Die Uhrenfedern werden auf einem vergoldeten Siliziumwafer galvanisiert, der mit einer lichtempfindlichen Farbe beschichtet ist (Bild: Empa)
Nebenprodukt der Forschungsarbeit
Doch für die Forscher der Empa ist diese Art Prototypenfertigung nur ein Nebenaspekt ihrer wissenschaftlichen Arbeit. Unser Ziel ist nach Aussage von Johann Michler keineswegs, mit Zulieferern der Uhrenindustrie in Konkurrenz zu treten. Die Forscher an der Empa interessiert vor allem der Prozess der Miniaturisierung an sich. Mit winzig kleinen Stempeln und Nadeln untersucht Michlers Team die mechanischen Eigenschaften der extrem kleinen Bauteile. Denn: Die Eigenschaften von Materialien ändern sich, wenn die Mechanik miniaturisiert wird: Duktile Metalle werden härter, während spröde Keramik dagegen teilweise duktil bei sehr kleinen Bauteilabmessungen wird.
Die Voraussetzung für jede Untersuchung ist, dass die Objekte, die getestet werden sollen, nach definierten Kriterien herstellt werden können, so der Empa-Forscher. Daher ist Michlers Team bestrebt, nicht nur einen einzigen Prozessschritt zu beherrschen, sondern die Qualität der gesamten Prozesskette in der Hand zu halten. Manche Verfahrensschritte hängen Michler zufolge eng zusammen. Wenn ein Parameter verändert wird, etwa die Geometrie der Galvanikformen oder die Zusammensetzung der Legierung, dann müssten meistens auch die vorausgehenden und nachfolgenden Schritte im Prozess angepasst werden. Die Forscher wollen die Zusammenhänge der Miniaturisierung in jedem Aspekt verstehen.
Additive Fertigungsverfahren in 3-D
Inzwischen gelang es den Forschern auch, Brücken und Säulen aus massivem Nickel herzustellen, die nur wenige Mikrometer groß sind. Belastungstests zeigen, wie sich die Nickellegierungen in diesen Dimensionen verhalten. Die Forscher können solche Strukturen bereits mit hoher Regelmäßigkeit und reproduzierbar herstellen. Auf dem Weg zur Mikromechanik aus galvanischen Bauteilen sind die Forscher nach ihrer Aussage ein großes Stück vorangekommen. Diese Bauteile könnten in nicht allzu ferner Zukunft Uhrwerke mit besonders feinen mechanischen Komplikationen möglich machen. Rainer Klose
www.empa.ch
Bild 3: Den Forschern gelang es, Brücken und Säulen aus massivem Nickel herzustellen, die nur wenige Mikrometer groß sind (Bild: Empa)