Edge-rounding and removing burrs of glass parts with laser radiation
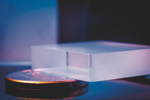
Part made of quartz glass, laser-polished and edge-rounded / Picture: Fraunhofer ILT / Volker Lannert, Aachen
The laser polishing process developed at the Fraunhofer Institute for Laser Technology ILT has been a well-known technique in metal and glass processing for several years now. It can be used not only for polishing surfaces, but also for rounding edges and for removing burrs e.g. split lines on parts formed by injection or compression molding. Rounding edges increases the stability of glass. Excess material protruding from the surface of injection or compression-molded parts can be removed so cleanly that it is no longer visible.
Rounding their edges can significantly increase the stability of glass parts. Laser polishing is an economical and fast technique for edge rounding of glass parts. When, as in laser polishing, a glass edge is processed with a CO2 laser, the material at the outermost surface layer heats up due to the surface near absorption of 80 percent of the laser radiation. A temperature just below its evaporation temperature is reached in the outher surface. This greatly decreases the viscosity of the material, while surface tension reduces the surface roughness. In contrast to conventional polishing techniques, no material is removed from the surface with laser polishing. In addition, the surface of the edge is polished. Subsequently, the edge surface and adjacent areas exhibit a very low level of micro-roughness. The result is not only greater stability in the edge region, but also a noticeable increase in the gloss level of the processed area. You can set the degree to which the edge is to be rounded and polished by means of the process temperature in the surface near layer, explains Annika Richmann, project manager at Fraunhofer ILT. Although parts are usually processed using a beam diameter of several millimeters, very local processing is also possible. Laser polishing can be used on virtually all types of glass, with greater process speeds obtainable for low-melting glasses.
The technique is also suited to removing burrs on glass and plastic injection and compression-molded parts. As in laser polishing, material is redistributed rather than removed; burrs are diminished to the point where they can no longer be seen or felt. This technique also greatly reduces the micro-roughness of the processed areas and heightens gloss.
Research at Fraunhofer ILT is presently focused on applying laser polishing techniques to freeform optics, where conventional polishing techniques are very slow. Lasers shorten processing times by a factor of up to 100, depending on the surface geometry to be polished. For many applications – including optical systems for illumination optics – the roughness values now obtainable are more than adequate. The challenge for the experts charged with further developing the laser polishing technique now consists in also attaining adequate roughness for imaging optics by means of further increasing shape accuracy and reducing waviness.
www.ilt.fraunhofer.de
Aktuelle Onlineartikel
-
20. 05. 2025 Korrosionsschäden an metallischen Bauteilen
-
15. 05. 2025 So entsteht die Optik der Zukunft – vom Glas zum System
-
15. 05. 2025 Neuer Kat verwandelt CO2 in einen Wertstoff
-
14. 05. 2025 KI vervielfacht Energiehunger von Rechenzentren
-
14. 05. 2025 Flüssiges Zinn entsalzt Meerwasser effektiv
-
13. 05. 2025 Neue Roboterhand packt zu wie ein Mensch