Wer in der Natur mit dem E-Bike unterwegs ist, hört lieber Vogelgezwitscher als störende Geräusche aus dem Antrieb des Elektrofahrrads. Laufruhe ist aber auch beim Elektroauto wichtig. Da der Elektromotor viel leiser arbeitet als ein Diesel oder Benziner, fallen unangenehme Geräusche bei der Fahrt stärker auf. Für Hersteller von Antriebskomponenten in der Elektromobilität bedeutet das: Die Ansprüche an die Oberflächengüte von Bauteilen, beispielsweise bei Zahnrädern, sind deutlich höher. Die E-Mobilität braucht mikroskopisch perfekte Oberflächen, um auch bei hohen Drehzahlen und Drehmomenten jederzeit die geforderte Laufruhe zu bieten. Auf der Fachmesse GrindingHub, die der VDW (Verein Deutscher Werkzeugmaschinenfabriken) vom 14. bis 17. Mai 2024 in Stuttgart veranstaltet, werden viele gute Lösungen dafür zu sehen sein.
Kraftvoll und zugleich kompakt muss der Antrieb für Elektrofahrzeuge sein – eine technische Herausforderung, für die extrem hochwertige Komponenten benötigt werden. Bei der Produktion der Zahnradmechanik für Elektroautos sind deshalb hochmoderne Fräs- und Schleifmaschinen gefragt. Sie arbeiten mit extremer Genauigkeit im Mikrometerbereich. Unter hoher Belastung entscheidet nämlich die Mikrogeometrie über das perfekte Ineinandergreifen der Zahnräder. Innovative Schleiftechnik ermöglicht sehr hohe Oberflächengüten, optimale Rundlaufeigenschaften und perfekte Zahnflankengeometrien. So wird auch gewährleistet, dass die Zahnräder an die Eigenfrequenzen des Antriebsstrangs angepasst werden können und dessen Schwingungen optimal dämpfen.
Mit seinen Wälzfräsen und Wälzschleifmaschinen trägt der GrindingHub-Aussteller Liebherr-Verzahntechnik GmbH aus Kempten im Allgäu dazu bei, dass Zahnradhersteller hochwertige Komponenten für Elektrofahrzeughersteller in bestmöglicher Qualität und hohen Stückzahlen liefern können. So ist ein effizienter, geräuscharmer und sauberer Getriebelauf garantiert. Reibungsminimierung und höhere Zahnflankentragfähigkeit stehen dabei im Fokus. Diese lassen sich mit Feinschleifen und Polieren gewährleisten.
Oberflächengüte auf höchstem Niveau
Die so genannten E-Antriebe weisen nach den Worten von Thomas Breith, Leiter Produktmanagement bei der Liebherr-Verzahntechnik GmbH, gegenüber den konventionellen Verbrennergetrieben weitergehende, in der Regel strenge Oberflächengüten der Verzahnungen auf; er nennt gleich mehrere Gründe dafür: erstens die geänderten Randbedingungen hinsichtlich der übertragbaren Leistungen und zweitens die hohen Schub-Drehmomente. Sie entstehen durch das so genannte Rekuperieren zur Wiedergewinnung von Energie beim Bremsvorgang. Auch die anspruchsvollen Anforderungen mit Blick auf hör- oder spürbare Schwingungen (Noise Vibration Harshness, NVH) erfordern eine hohe Oberflächengüte der Verzahnungen. Und nicht zuletzt sorgen reduzierte Rauigkeitswerte für eine bessere Batteriereichweite. Die Verzahnungs-Qualität wird deshalb in allen Beziehungen auf ein höchstes Niveau gehoben, wie Breith betont.
Thomas Breith, Leiter Produktmanagement bei Liebherr-Verzahntechnik GmbH (Bild: Liebherr-Verzahntechnik)
Exakte Vorgaben für Rauigkeit
Aber wie lassen sich die erhöhten Anforderungen bei der Fertigung der Getriebekomponenten erfüllen? Die Erstausrüster (Original Equipment Manufacturer, OEM) geben den Zulieferern die möglichen Herstellungsverfahren weitgehend vor, indem sie bestimmte Oberflächen-Sollwerte für die Rauigkeit festlegen. Diese sind in internationalen Normen definiert, etwa Mittlere Rauheit (Ra), maximale Höhe des Profils (Rz), Kernrautiefe (Rk), reduzierte Spitzenhöhe (Rpk) oder reduzierte Riefentiefe (Rvk). Hohe, aber noch schleifbare Oberflächengüten werden durch das so genannte Feinschleifen mit Duoschleifschnecken sichergestellt. Bei diesen Werkzeugen werden je Schleifhub verschieden optimierte Schleifschnecken-Spezifikationen zum Einsatz gebracht, erklärt Breith. Das Ergebnis sind geometrisch hochpräzise Verzahnungs-Geometrien gemäß den DIN- beziehungsweise ISO-Auswertungen auf den Verzahnungs-Messgeräten. Die Rz-Werte liegen zwischen 1,2 und 1,8 Mikrometer.
Mit feiner Schleifschnecke und Polierschnecke
Werden seitens des OEMs noch höhere Rz-Werte zwischen 0,8 und 1,2 Mikrometer gefordert, kommt laut Breith das so genannte Polierschleifen zum Tragen. Der Schneckenbereich weist dann eine sehr feine Schleifschnecke und eine Polierschnecke auf. Der Polierschnitt könne dann jedoch nur einen Abtrag von 2 bis 3 Mikrometer auf der Zahnflanke sicherstellen. Der Prozess muss im Auftragsfall von Bauteil zu Bauteil in einem Vorversuch optimiert werden, wobei ein Abgleich der Messmittel zwischen dem Hersteller und dem Endanwender unerlässlich ist, so der Liebherr-Manager.
Viele Herausforderungen sind zu meistern, um ein perfektes Ergebnis zu erzielen. Laut Thomas Breith ist die Grundvoraussetzung eine hochpräzise Verzahnungsschleifmaschine, die über die zusätzlich erforderliche Anwendungssoftware verfügt. Die Optimierung des Prozesses werde durch eine kompetente Anwendungstechnik seitens des Maschinenherstellers umgesetzt. Die Prozesssicherheit sei nur mit sehr hochwertigen Spannmitteln und Schleifwerkzeugen möglich. Dazu sei das Know-how des Herstellers wichtig, eine intensive Kundenbetreuung werde vorausgesetzt.
Wettbewerbsvorteile dank innovativer Technik
Mit der Umstellung von Verbrennungsmotoren auf Elektroantriebe werden zwar künftig weniger Zahnräder und damit geringere Stückzahlen benötigt. Dafür steigen jedoch die Qualitätsanforderungen an die Zahnradhersteller, so dass Investitionen in innovative und flexible Technik, die auch kleine Stückzahlen bewältigt, lohnend sein können. Zulieferer, die sich für die flexible Produktion von hochfeinen Oberflächen bei unterschiedlichen Konturen rüsten, können sich bei weiterhin steilen Wachstumsraten in der Elektromobilität somit Wettbewerbsvorteile und einen schnellen Return on Investment sichern.
Auch die Emag GmbH mit Sitz im schwäbischen Salach bietet besonders präzise und prozesssichere Schleiflösungen für den Einsatz in der Elektromobilität an. Die Technik soll ebenfalls höchste Oberflächengüten ohne störende Laufgeräusche garantieren. Vor diesem Hintergrund rückt der deutsche Werkzeugmaschinenbauer die Technologie der Tochtergesellschaft Emag SU aus Mailand in den Fokus der Produktionsplaner und zeigt diese auf der GrindingHub. Die Spezialisten aus Italien entwickeln unter anderem Hochleistungslösungen für das Verzahnungsschleifen.
Durch besonders präzise Schleiflösungen für den Einsatz in der E-Mobilität werden höchste Oberflächengüten im Mikrometerbereich gewährleistet; sie sorgen dafür, dass an den Verzahnungsbauteilen keine störenden Laufgeräusche entstehen (Bild: Emag)
Bei der Schleifanlage G 160 erzeugt die vorhandenen Y- und Z-Achsen durch simultane Bewegung eine virtuelle Tangentialachse, wodurch die Oberflächengüte perfektioniert wird (Bild: Emag)
Keine Angst vor Geisterfrequenzen
Oliver Hagenlocher, Leiter Marketing von Emag, führt als herausragende Lösungen für die Verzahnungsschleifbearbeitung Wälzschleifmaschinen mit innovativem Achskonzept an. Dieses sorgt für die in der E-Mobilität so wichtigen perfekten Oberflächen. Entscheidend ist dabei, dass die Wälzschleifmaschine nicht über eine Tangentialachse verfügt, sondern die vorhandenen Y- und Z-Achsen durch eine simultane Bewegung eine virtuelle Tangentialachse erzeugen. Daraus folgt, dass der Abstand zwischen A-Achse und Werkzeugkontaktpunkt sehr klein ist, was wiederum die so genannten Geisterfrequenzen auf der Oberfläche des Bauteils verhindern soll.
Was gespenstisch klingt, hat rationale Gründe. Bei Geisterfrequenzen handelt es sich um Frequenzen, die nicht mit den Zahneingriffsfrequenzen und deren Vielfachem zusammenfallen und die auch beim Schleifen in das Bauteil eingebracht werden können. Ursachen für Geisterfrequenzen sind minimale Unregelmäßigkeiten, die in der Serienfertigung kaum zu vermeiden sind. Besonders kritisch wird es, wenn diese Abweichungen dazu führen, dass es zu einer harmonischen Anregung kommt. Es ist viel Know-how und Prozesserfahrung nötig, um die Gründe für solche Unregelmäßigkeiten zu erkennen und zu vermeiden.
Angenehmes Summen statt nervtötender Geräusche
Wie bei Elektroautos ist auch bei E-Bikes eine optimale Oberflächenqualität der Bauteile für den Antrieb sinnvoll, allerdings in nicht ganz so hohem Maß. Die derzeitigen E-Bike-Anwendungen spiegeln nach Aussage von Thomas Breith noch nicht die Qualitätsanforderungen der bisher vorliegenden Pkw-E-Antriebe wider. Dem Liebherr-Manager zufolge ist es jedoch auch beim Elektrofahrrad nicht ausgeschlossen, dass bestimmte Verzahnungskriterien in Zukunft einer ähnlichen Steigerung wie im Automotive-Bereich folgen werden.
Für Zulieferer, die bei der Elektromobilität vorne mitspielen wollen, ist daher hochpräzise und moderne Fertigungstechnik unabdingbar. Denn nur mit perfekt geschliffenen Bauteilen fahren Elektroautos und E-Bikes mit maximaler Effizienz und summen im Einsatz, statt nervtötende Geräusche zu produzieren. Daniel Schauber

Text zum Titelbild: Wälzschleifen eines Abtriebzahnrads für einen E-Antrieb mit abrichtfreiem CBN; abrichtfreie CBN-Schleifschnecken der Liebherr-Verzahntechnik bieten eine hohe Prozessstabilität durch lange Werkzeugstandzeiten, Vermeidung von Fehlerquellen beim Abrichten, einfaches Werkzeughandling sowie deutlich reduzierten Mess- und Prüfaufwand (Bild: Liebherr-Verzahntechnik)

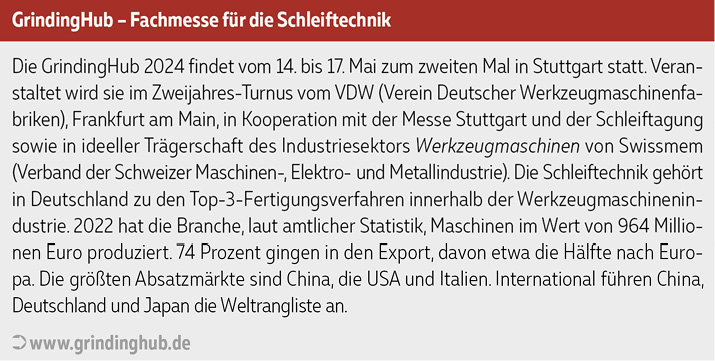