Sowohl bei der spanenden als auch bei der umformenden Bearbeitung entstehen Kühlschmiermittelemissionen, die zum Schutz der Mitarbeiter reduziert werden müssen. Ein neues Filtersystem erzielt dabei so reine Luft, dass sie in das Arbeitsumfeld zurückgeleitet, abgeschiedenes Kühlschmiermittel zurückgewonnen und der Instandhaltungsaufwand minimiert werden kann. Dies reduziert Betriebskosten und optimiert sowohl Hallenklima als auch Nachhaltigkeit.
Bei der Fertigung von Kupplungen aus metallischen und nicht-metallischen Materialien für Pneumatik- und Fluidanwendungen sowie von Sonderlösungen für unterschiedliche technologische Bereiche läuft in der Zerspanung der Lüdecke GmbH ohne Kühlschmiermittel (KSS) nichts. Und je schneller gearbeitet wird, desto mehr KSS-Emissionen in Form von Aerosolen, Dämpfen und Rauch bilden sich, die eine Gefahrenquelle für die Gesundheit der Mitarbeiter darstellen können. Entsprechend existieren behördliche Vorschriften, dass Kühlschmiermittelemissionen am Arbeitsplatz bestimmte Grenzwerte nicht überschreiten dürfen. Die emissionsbeladene Abluft wird daher mit einem Abscheidesystem abgesaugt, gereinigt und häufig ins Freie abgeführt. Und mit ihr die Wärme, was insbesondere im Winter kostspielige Energieverluste verursacht.
Diese unwirtschaftliche Vorgehensweise war nur ein Grund, weshalb man beim Kupplungs- und Armaturenhersteller Lüdecke entschieden hat, die Kühlschmierstoffabscheidung in einem neu gebauten Hallenbereich nach neuesten technologischen Standards auszulegen. Dafür wurde gemeinsam mit der Herding GmbH Filtertechnik ein Konzept für 17 Maschinen aus der spanenden Fertigung erarbeitet. Abgestimmt auf das Nachhaltigkeitskonzept des Unternehmens enthielt der Forderungskatalog auch eine Verbesserung des Arbeitsumfelds bei gleichzeitiger Verringerung des Wartungs- und Instandhaltungsaufwands. Umgesetzt wurden diese Anforderungen mit einer innovativen Komplettlösung für das Abscheiden von Kühlschmierstoff aus der abgesaugten Luft von der Herding GmbH Filtertechnik.
Reinluftrückführung und KSS-Rückgewinnung
Das Herz der neuen Filteranlage, die auf der flexiblen und kompakten Baureihe Herding FLEX basiert, ist ein dreistufiges Filtersystem. Die von den Maschinen abgesaugte Luft wird zunächst durch einen Drallabscheider geleitet. Größere Öltropfen werden hier durch Fliehkraft aus der Luft abgeschieden und setzen sich an der Wandung des Abscheiders ab. Dieses Öl kann direkt in die Kühlschmiermittelversorgung zurücktransportiert werden.
Die vorgereinigte Luft gelangt anschließend in die Hauptfilterstufe. Sie ist mit speziellen von Herding entwickelten Sinterlamellen-Filterelementen aus gesintertem Polyethylen ausgestattet. Sie bieten bei hoher mechanischer Stabilität eine sehr hohe Abscheideleistung. Da die Sinterlamellenfilter vollkommen faserfrei sind, kann auch hier das abgeschiedene Kühlschmiermittel zurückgewonnen werden. Vereinfacht wird dies durch die automatische Reinigung der Filterelemente im Gegenstromverfahren mit Druckluft im laufenden Betrieb. Dabei wird das abgeschiedene Kühlschmiermittel nach außen gedrückt und läuft ab.
Als dritte, in das Filtergehäuse integrierte Stufe durchläuft die Luft einen Schwebstofffilter der Klasse H13, die beispielsweise auch für die Luftfiltration in Reinräumen eingesetzt wird. Das Reingas ist dann schon so gut von Emissionen und Partikeln befreit, dass bei Lüdecke der Schwebstofffilter selbst nach über einem Jahr Betriebszeit noch nicht gewechselt werden musste.
Durch die dreistufige Filtration wird ein Abscheidegrad von mindestens 99,95 Prozent erreicht, womit die gesetzlichen Vorgaben unterschritten werden. Die gereinigte Luft kann daher einfach in die Halle zurückgeführt werden. Daraus resultieren nicht nur energetische Vorteile, sondern es sind auch keine aufwendigen Deckendurchbrüche, Kamine und Rohrleitungen für die Luftabführung ins Freie erforderlich. Darüber hinaus ergeben sich durch die Kühlschmiermittelrückgewinnung Einsparungen. Sie betragen bei Lüdecke, wo inzwischen fünf Filtersysteme im Einsatz sind, mindestens 7000 Liter Schneidöl pro Jahr, was rund 15 Prozent des Gesamtverbrauchs entspricht.
Optimal angepasst und energieeffizient
Die Auslegung des Abscheidesystems zählt zu den komplexesten Aufgaben beim Einsatz von Kühlschmierstoffen. Bei Herding werden die Anlagen daher auf die jeweilige Anwendung maßgeschneidert. Dies schließt sowohl die Anpassung des Absaugvolumens als auch die Verrohrung ein. Bei Lüdecke liegt das Absaugvolumen bei 250 Kubikmeter Luft pro Maschine und Stunde, was sich zu einem Gesamtabsaugvolumen von rund 5000 Kubikmeter Luft pro Stunde summiert. Um den Luftstrom an den tatsächlichen Bedarf anzupassen, beispielsweise wenn nicht alle Maschinen gleichzeitig in Betrieb sind, und dadurch Energie einzusparen, ist der Ventilator mit einem frequenzgesteuerten IE3-Motor ausgestattet.
Das Rohrsystem wird ebenfalls an die jeweiligen Verhältnisse angepasst. Dabei spielt zum einen das Saugvolumen der Anlage eine Rolle. Andererseits ist der Bauraum der angeschlossenen Maschinen ein entscheidender Faktor. Bei in Reihe stehenden Anlagen trägt eine sich verjüngende Rohrleitung zu einem energieeffizienten Betrieb bei.
Ein weiterer Aspekt, der bei zentralen Absaugsystemen unter versicherungstechnischen Gesichtspunkten nicht vernachlässigt werden darf, ist der Brandschutz. Herding stattet daher die Verrohrung der Absaugsysteme mit Temperatursensoren aus. Wird eine definierte Temperatur überschritten, schließt eine weit vor der Filteranlage platzierte Brandschutzklappe automatisch und die betreffende Maschine wird automatisch heruntergefahren.
Hohe Anlagenverfügbarkeit durch geringen Instandhaltungsaufwand
Zum geringen Wartungs- und Instandhaltungsaufwand der Anlage trägt neben der guten Abscheideleistung und automatischen Selbstreinigung der mechanisch stabilen, regenerier- und recycelbaren Sinterlamellenfilter deren lange Standzeit von bis zu 15 Jahren bei. Eine Differenzdrucküberwachung stellt sicher, dass bei gesättigten Elementen der erforderliche Wechsel in der Anlagensteuerung angezeigt wird. Da sämtliche Filter gut zugänglich sind, kann ein Wechsel der Sinterlamellen-Filterelemente in weniger als 30 Minuten erfolgen. Das Filterelement des Schwebstofffilters lässt sich in noch kürzerer Zeit austauschen. Die Maschinenstillstandszeiten werden dadurch auf ein Minimum verringert.
Kontakt
Herding GmbH Filtertechnik, Markus Mußemann
Lüdecke GmbH, Simon Lottner
- www.herding.de
- www.luedecke.de

Kompaktes Kühlschmierstoff-Absaugsystem mit drei integrierten Filterstufen für die Rückführung der gereinigte Luft in die Halle und Rückgewinnung von abgeschiedenem Kühlschmiermittel
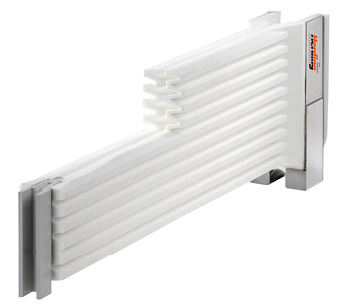
Die mechanisch stabilen, regenerier- und recycelbaren Sinterlamellen-Filterelemente bieten eine hohe Abscheideleistung und eine Standzeit von bis zu 15 Jahren
Text zum Titelbild: Bei Lüdecke sind 17 Zerspanungsmaschinen an eine Filteranlage angeschlossen, die eine deutlich Energieeinsparung garantieren und für einen wirtschaftlichen Betrieb sorgen