Von Filipp Pachomow, Maulbronn
Metallverarbeitende Betriebe, insbesondere Automobilzulieferer, stehen seit jeher unter großem Kostendruck: Die generelle Erwartungshaltung der Kunden geht seit Jahren in Richtung Preisreduzierung. Wer seine Produktion nicht ins Ausland verlagern will, versucht, die Produktivität zu steigern. Großes Potential liegt dabei zweifellos in der Automatisierung der Produktionsprozesse. Nachdem die größten Anwendungsfelder wie Schweißen oder Handling bereits weitgehend automatisiert sind, rücken vermehrt auch Nischenanwendungen, wie etwa das Entgraten, in den Fokus. Dieses gilt seither als nicht wertschöpfend, lässt sich aber bei vielen Herstellungsprozessen nicht vermeiden. Eine der kostengünstigsten Automatisierungslösungen ist dabei das roboterbasierte Entgraten mit Druckluftspindeln. Auf diese Nische hat sich das 1919 gegründete schwäbische Familienunternehmen Schmid & Wezel GmbH aus Maulbronn spezialisiert, dass unter der Marke BIAX Druckluftspindeln herstellt und vertreibt.
Eines von vielen Beispielen für eine gelungene Prozessautomatisierung liefert die IDS Casting Service GmbH aus Oggelsbeuren auf der schwäbischen Alb. IDS ist ein Lohnfertiger, der täglich mehrere tausend Aluminiumdruckgussteile der Albert Handtmann Metallgusswerke GmbH aus Biberach in vier Roboter-Entgratzellen bearbeitet. Noch vor einigen Jahren wurde manuell entgratet, bis Reinhard Maier, kaufmännischer Leiter bei IDS, die Automatisierung selbst in die Hand nahm. Seither arbeitet IDS dreimal schneller und zweimal günstiger, als von Hand. Hinzu kommt, dass es fast keinen Ausschuss mehr gibt und die Qualität des Arbeitsergebnisses konstant bleibt. Doch nicht jeder Betrieb verfügt über versierte Spezialisten und ausreichendes Know-how, um ein Automatisierungsprojekt aus eigener Kraft zu stemmen. In diesem Fall bietet sich die Zusammenarbeit mit externen Systemintegratoren an. In jedem Fall ist es hilfreich, einige grundsätzliche Dinge über das roboterbasierte Entgraten zu wissen.
Aufbau einer Entgratzelle
Die Entgratzelle mit Roboter ist normalerweise fester Bestandteil einer automatisierten Transferstraße. Die zu entgratenden Bauteile werden dabei automatisch dem Roboter zugeführt. Dieser greift dann Teil für Teil und führt es zu einer oder mehreren fest installierten Spindeln. Würde der Roboter die Spindel führen, müsste jedes einzelne Bauteil erst einmal fixiert werden, was einen unnötigen Zeitverlust darstellt. Daher findet dies nur bei sehr großen Bauteilen Anwendung. Es werden bevorzugt druckluftbetriebene Spindeln eingesetzt, da sie im Vergleich zu Elektrospindeln deutlich preiswerter, vom Gewicht her leichter und kompakter sind. Auch lassen sich mit Druckluftspindeln viel höhere Geschwindigkeiten erzielen, als mit Elektrospindeln.
Die verschiedenen Werkzeuge und Spindelarten
Grundsätzlich lassen sich, je nach Werkstück und gewünschtem Ergebnis, sehr unterschiedliche Bearbeitungswerkzeuge, wie Frässtifte, Bürsten, Feilen, Senker und Schleifkörper, einsetzen. Am häufigsten verbreitet ist sicherlich das Entgraten mit Frässtiften und Bürsten für feste beziehungsweise lose Grate. Feilen kommen meist dann zum Einsatz, wenn nur ein sehr geringer Materialabtrag erlaubt ist. Senker werden zum Entgraten von Bohrungen verwendet.
Die Spindeln können starr sein oder mit einer radialen beziehungsweise axialen Auslenkeinheit eingesetzt werden. Die Auslenkeinheit wird insbesondere dann erforderlich, wenn Bauteiltoleranzen und Ungenauigkeiten in der Positionierung des Werkstücks ausgeglichen werden müssen. Ersteres ist gerade für Gussteile typisch, egal ob aus Metall, Kunststoff oder Faserverbundwerkstoff, da diese im Gegensatz zu Graten von bearbeiteten (zerspanten) Teilen in der Regel sehr ungleichmäßig sind. Die Auslenkung wird pneumatisch oder über Federpakete erzeugt, die Auslenkkraft lässt sich über Druck oder Federvorspannkraft einstellen.
Das optimale Ergebnis und Hindernisse
Martin Erle, Automatisierungsexperte bei BIAX, definiert das optimale Ergebnis beim automatisierten Entgraten wie folgt: einegleichmäßige und gleichbleibende Entfernung des Grates bei sich wiederholenden Bauteilen. Beispielsweise wird durchgängig eine Fase von 0,5 mm erzeugt und diese Fase ist bei allen Bauteilen identisch. Diverse Faktoren wie das Werkzeugsystem, die Bauteiletoleranz, die Beschaffenheit des Grates, der Roboter und seine Programmierung sowie die Spannmittel beziehungsweise der Greifer, haben Einfluss auf die Genauigkeit des Ergebnisses. Zu den häufigsten Entgrataufgaben gehört die Entfernung eines losen Grates oder das Erzeugen einer undefinierten Phase. Hierfür empfiehlt Erle grundsätzlich die Verwendung eines flexiblen Systems (Bürste, Feile und/oder Auslenkung).
Bei nur geringer Bauteil- und Positionstoleranz sollte aber ein starres System eingesetzt werden, da es sauberer und genauer arbeitet, ein besseres Ergebnis bringt und in der Anschaffung günstiger ist. In diesem Fall kann sogar eine definierte Fase reproduziert werden. Problematisch wird es nach Erfahrung des Experten aus Maulbronn erst, wenn bei großen Toleranzen eine definierte Fase erzeugt werden soll. Hierfür gibt es zwar einige Lösungsansätze, diese sind nach Aussage von Erle aber (noch) sehr aufwendig und heben den Produktivitätsgewinn der Automatisierung wieder auf. Denkbar wären etwa der Einsatz von Werkzeugen mit Festanschlag, die Verwendung von mehreren Bearbeitungsschleifen oder eine exakte Vermessung (Scan) der Bauteillage/Bauteilmaße eines jeden Bauteils.
Eine Zusammenfassung der verschiedenen Anforderungen und Lösungsmöglichkeiten in Kombination mit verschiedenen Faktoren ist in der BIAX-Anwendungsmatrix aufgezeigt. Das flexible System steht dabei für eine Spindel mit Auslenkung.
Kurzcheck als Service: Möglichkeiten zur Automatisierung des Entgratprozesses
Für Interessenten, die ihre Entgratprozesse automatisieren möchten, bietet BIAX einen kostenlosen Beratungsservice: Nach Einsendung des Bauteils prüfen die Maulbronner die Machbarkeit mit ihrem hauseigenen Fanuc Roboter und geben eine konkrete Empfehlung hinsichtlich Werkzeug, Spindel und Vorschubgeschwindigkeit ab. Das sind sehr wertvolle Informationen, die bei der Programmierung viel Zeit und Geld sparen können. Auch eine Beratung vor Ort ist möglich, wenn das Bauteil nicht herausgegeben werden darf.
Dass BIAX auch eine Vielzahl verschiedenster Entgratspindeln anbietet, versteht sich dabei von selbst. So hat man jüngst mit dem RSC Modular System ein einzigartiges Entgratsystem nach dem Baukastenprinzip auf den Markt gebracht: Hiermit lässt sich in Abhängigkeit von der Anwendung eine individuelle Lösung zusammenstellen. Man zahlt also nur für das, was man wirklich braucht und kann später kostengünstig nach- beziehungsweise umrüsten.
Es gibt verschiedene gerade und gewinkelte Druckluftspindeleinsätze mit Geschwindigkeiten von 10 000 bis 100 000 Umdrehungen pro Minute sowie eine oszillierende Spindel für Feilen. Diese werden immer in ein Kupplungsteil eingesetzt. Optional stehen eine radiale und eine axiale Auslenkung zur Verfügung. Neben den Beschaffungskosten verringern sich auch die Lagerkosten, da nur die Spindeleinsätze und nicht das komplette System für den Notfall vorgehalten werden muss.
BIAX auf der DeburringEXPO 2017
Halle 1, Stand 321
- www.biax.de
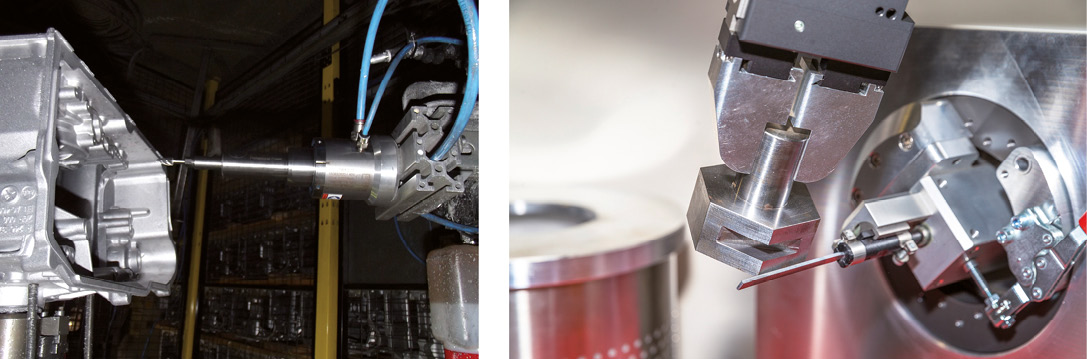
Entgraten mit fest installierter Spindel mit Auslenkung, bei der der Roboter das Bauteil führt (links) und Entgratzelle mit Druckluftfeile (rechts)

RSC-System am Roboter und fixiertem Bauteil