GF Machining Solutions setzt erneut einen Meilenstein in der Senkerosion. Die innovative 3DS-Technologie verspricht Nutzern von Spritzgussformen wesentliche Produktivitätssteigerungen – dank besserer Entformbarkeit, schnellerer Produktionszyklen und reduzierter Wartungskosten. Der Werkzeugbauer Lauer Harz setzt die neue Technologie seit kurzem ein.
Der Werkzeugspezialist Lauer Harz GmbH beschäftigt rund 30 Mitarbeiter in Lüdenscheid
3DS-Bearbeitungszentrum von GF Machining Solutions bei Lauer Harz
Mit der Funkenerosion lassen sich leitfähige Werkstoffe beliebiger Härte hochpräzise und mit höchster Oberflächengüte bearbeiten. Mehr als jedes andere Maschinenbauunternehmen hat GF Machining Solutions dieses Verfahren im Laufe der letzten 50 Jahre ständig perfektioniert. David Labadie, bei GF Machining Solutions für die Produktlinie Senkerosion verantwortlich, stellt fest, dass viele potenzielle Anwender davon ausgehen, dass die Möglichkeiten dieser Technologie inzwischen weitestgehend ausgereizt sind. Doch die Ingenieure des GF Innovations-Teams sind im Begriff, mit den neuen 3DS-Erosionsoberflächen die EDM-Technologie zu revolutionieren.
Das Kürzel 3DS steht für dreidimensionale Strukturen. Tatsächlich beschreitet dieser Ansatz einen neuen Weg: Wurde bislang die Qualität einer Oberfläche im Grad ihrer zweidimensionalen Rauheit bewertet (Ra-Wert), betrachtet die 3DS-Technologie die tatsächliche, dreidimensionale Beschaffenheit einer Oberfläche.
Werkzeugoberflächen können nach Aussage von Joachim Seele, Leiter Sales Support bei GF Machining Solutions, den gleichen Ra-Wert haben und dennoch gänzlich unterschiedliche Eigenschaften aufweisen. Mit der 3DS-Technologie erhalten Werkzeugbauer und vor allem Spritzgießer ganz neue Möglichkeiten. Dank einer optimierten Funkenentladung beim Erosionsprozess werden die Oberflächen wesentlich entschärft. Die Erodiertiefen sind zwar noch vorhanden, dreidimensional betrachtet weisen sie aber ein deutlich verrundetes Profil auf, wie der EDM-Experte ausführt.
Konkrete Vorteile dank 3DS
Was zunächst sehr theoretisch klingt, birgt entscheidende Vorteile für Anwender der 3DS-Technologie. Das bestätigt Kurt Harz, Geschäftsführer der Lauer Harz Werkzeugtechnologie GmbH. Das mittelständische Unternehmen aus dem sauerländischen Lüdenscheid stellt seit über 25 Jahren Spritzgussformen her – vornehmlich für die Automobil-, Pharma- und Bauindustrie. Feinwerkmechanikermeister Harz setzt seit jeher auf Maschinen von GF Machining Solutions und hat in seiner Laufbahn stets ein gutes Gespür für Innovationen bewiesen. Als kleiner Werkzeugbauer kann er sich nach eigenem Bekunden keine Fehlgriffe erlauben und prüft die Anschaffung neuer Maschinen sehr genau. Sie müssen dem Unternehmen einen Wettbewerbsvorteil verschaffen, der sich schnell in Kostenvorteilen auszahlt. So hat er sich als einer der ersten Kunden von GF Machining Solutions dazu entschieden, die neuartige 3DS-Technologie einzuführen. Kurt Harz hat im Frühjahr 2015 ein Komplettsystem von GF Machining Solutions angeschafft, ein so genanntes FORM Werk. Es besteht aus einer Highspeed-Fräsmaschine Mikron HSM 500 LP, einem Roboter, einer Jobmanagement-Software und dem Herzstück, einer Senkerosionsmaschine AgieCharmilles Form 200 mit 3DS-Funktion.
Ein Hälfte der Oberfläche wurde mit 3DS und die andere herkömmlich erodiert; obwohl beide Flächen denselben Ra-Wert haben, unterscheiden sie sich optisch deutlich voneinander
Innovative Senkerodiertechnologie überzeugt schnell
In den ersten Tagen waren Kurt Harz und seine Facharbeiter noch etwas skeptisch. Was sollte sich am lange erprobten Erodiervorgang noch verbessern lassen, fragte sich die eingeschworene Werkzeugbauertruppe. Sie experimentierten, fertigten erste Prototypen an und waren von den Ergebnissen verblüfft: Die Scharfkantigkeit der Erodierkrater gehörte plötzlich der Vergangenheit an, wodurch das Entformen der dünnen Stege deutlich einfacher wurde. Mit 3DS konnten die realen Entformkräfte mehr als halbiert werden. Eine manuelle Nacharbeit der Formen, wie beispielsweise Handpolitur, war kaum noch erforderlich.
Doch nicht genug: Die 3DS-Technologie von GF Machining Solutions eliminiert auch den sogenannten Dieseleffekt nahezu vollständig. Die perfekt verrundete Oberfläche des Werkzeugs begünstigt die Entlüftung beim Spritzguss. Gaseinschlüsse werden somit vermieden, was wiederum Dieseleinbränden vorbeugt. In der Konsequenz müssen 3DS-Formen nicht so oft gereinigt werden und sind damit deutlich produktiver. Insgesamt ergeben sich viele Vorteile für den Endkunden, wie Joachim Seele, GF Mitarbeiter seit 21 Jahren, erklärt: Je leichter das Entformen vonstatten geht, desto wärmer kann der Kunststoff beim Entformungsprozess sein. Entsprechend weniger Zeit benötigt das Abkühlen. So konnte beispielsweise beim Unternehmen Bernd Richter in Wipperfürth die Abkühlzeit von 65 auf 30 Sekunden mehr als halbiert beziehungsweise die Ausbringung der Maschine verdoppelt werden. Die Produktivitätssteigerungen sind also erheblich.
Mikroskopische Aufnahme einer erodierten Oberfläche, die in beiden Fällen denselben Ra-Wert 0,8 µ aufweist; in der unruhigeren Topograhie der linken Fläche ohne 3DS verhakt sich der Kunststoff und lässt sich so deutlich schwerer entformen als in der oberen, deutlich homogeneren Fläche, die mit der 3DS-Technologie hergestellt wurde
Zudem tritt nach Kenntnis von Kurz Harz der Dieseleffekt kaum mehr auf. Tatsächlich ist dieses Argument nicht von der Hand zu weisen: Bei bestimmten Kunststoffarten – zum Beispiel jenen mit hohem Glasfaseranteil – ist ohne 3DS-Technologie eine gründliche Reinigung der Spritzgussmaschine mittels Trockeneisstrahlen alle vier Stunden notwendig. Dank der 3DS-Technologie verlängert sich der Zyklus von viereinhalb auf deutlich über zehn Stunden. So können die Kunden der Lauer Harz GmbH die Maschinen auch über Nacht laufen lassen und erhöhen so die Wirtschaftlichkeit.
Und es gibt noch einen weiteren Unterschied: Mit 3DS ist die Oberfläche des Spritzgussteils weniger empfindlich gegen Kratzer. Was diese Technologie gerade auch für die Produktion von empfindlichen und beanspruchten Sichtteilen sehr interessant macht. Ideale Einsatzfelder sind zum Beispiel Armaturen, Verkleidungen, Abdeckungen und Griffe für das Fahrzeuginterieur, Haushaltsgeräte und die Verpackungsindustrie bis hin zu Handyschalen.
Visionär im Sauerland
Werden die Vorzüge der neuen 3DS-Technologie betrachtet, so ist davon auszugehen, dass sie sich schnell als Standard in der Industrie durchsetzt, ist Kurt Harz überzeugt. Innovationen setzen sich meist von unten durch. Die 3DS-Technologie von GF Machining Solutions gilt noch als Geheimtipp, noch... Wie gesagt, Kurt Harz hat ein gutes Gespür für erfolgreiche Innovationen.
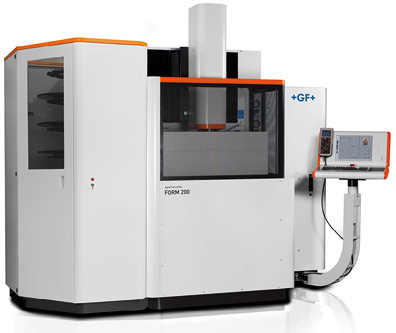
Das FORM Werk von GF Machining Solutions besteht aus einer Senkerodiermaschine AgieCharmilles FORM 200, einer Highspeed-Fräsmaschine Mikron HSM 500 LP und einem Palettenwechsler WorkPartner 1+ – eine kompakte Automationslösung für den Werkzeug- und Formenbau zur Elektrodenherstellung und zum Hartfräsen von Werkzeugkomponenten
